Four common misunderstandings about Sage Oil Vac products explained
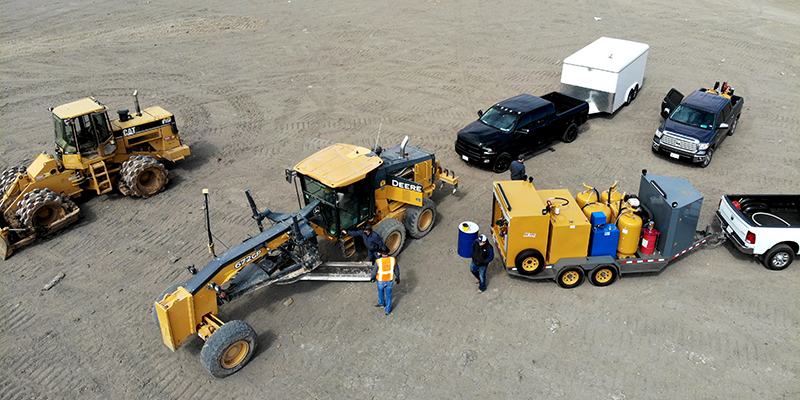
Let’s talk about some common misunderstandings and concerns we often hear about Sage Oil Vac fluid exchange systems. That’s right, we’re putting ourselves in the hot seat to clear up the most popular misconceptions about our product lines — after all, we’re the ones who know it best.
How Sage Oil Vac systems work
(Feel free to skip this section if you’re familiar with our brand — or watch our video.)
Pump-based oil extraction equipment has been the industry standard for decades, but that’s only because it’s what people have always known, not because it’s the greatest way to achieve the end results. Pump-based equipment needs constant, high-volume compressed air while you’re operating, Sage Oil Vac systems do not.
Sage fluid exchange systems use a patented pump-free design, allowing the end-user to dispense and drain fluids faster using cutting-edge vacuum technology. Compressed air builds vacuum and or pressure to move fluids to and from tanks. Our system goes against the grain of the traditional pump-based technology, offering customers who make the switch a cleaner, more energy-efficient oil change on the job.
Setting the record straight
Misconceptions No. 1 and No. 2:
Sage Oil Vac systems require more air compressor run time and are louder than pump-based oil extraction equipment.
Let’s tackle these two together. Sage Oil Vac systems actually use less compressor run time than pump-based equipment. Our systems conserve air by creating and maintaining vacuum pressure within the tanks. When using Sage Oil Vac systems out on the jobsite, you can either pressurize your tanks in the shop with compressors before you leave or on the jobsite with a gas or diesel powered air compressor that can be added to your Sage model. This is compared to conventional air pump systems which need to run air compressors 100% of the time.
Once you have the necessary air pressure to dispense new oils or drain used oils, the compressor can be turned off. Sage Oil Vac professionals advise operators to turn off machines once 20 inches (50.8 cm) of vacuum has been captured in the waste tank and 60-80 psi in the fresh oil tank. Using this advice ensures that Sage Oil Vac systems reduce air compressor run time by up to 70% over conventional pump-based equipment, and therefore reduce overall air usage.
This practice minimizes the amount of wear and tear on equipment and significantly lessens onsite noise and — in some cases — added emissions. Our product operators often comment they enjoy the quietness of their Sage Oil Vac system. Without needing a compressor to run the entire time or experiencing the noises from diaphragm/piston pumps, their workday fatigue improves.
Misconception No. 3:
Sage Oil Vac systems require and use more pressure than pump-based oil extraction equipment.
Pump-based equipment uses waves of pressure to extract/insert oil versus the Sage Oil Vac system, which uses constant vacuum pressure to pull/push oil. This equates to less fluid pressure per square inch (psi) usage. A diaphragm pump system with one piston pump generates 500 psi in pulses. Our system uses 60-80 psi of steady pressure. Reduced psi requirements almost always correlate with reduced risks for machine malfunction.
Misconception No. 4:
Sage Oil Vac systems weigh more than a conventional pump system.
Sage Oil Vac systems actually weigh less, as they don’t have the weight of a pump added to each tank. The lighter weight of Sage Oil Vac systems makes it easier for our engineers to create a non-CDL truck option to meet increasing industry demand for more lube bodies and service truck options that do not require a CDL.
How did we do? Do you have more questions? Contact the Sage Oil Vac team to learn more.