Three Ways a Dedicated Lube Technician Can Boost Efficiency and Profits
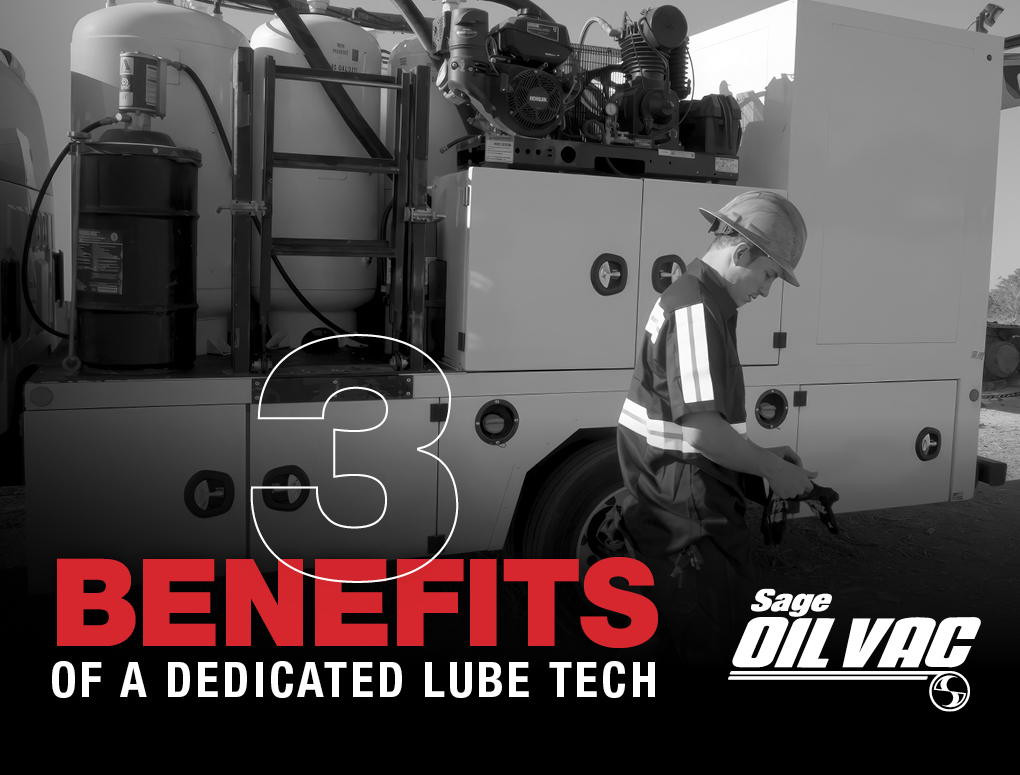
Preventive maintenance is a crucial part of your business. But it can feel like a hassle if you rely on third-party vendors to get it done (or you’re allocating skilled mechanic time to a relatively simple job). If that sounds familiar, a dedicated lube technician could be the solution you’re looking for. Let’s explore three reasons construction companies are adding them to their teams.
1. They help you control your schedule and avoid downtime.
Hiring a third-party company to handle preventive maintenance seems convenient until you see service delays, inconsistent results, and coordination headaches. On the other hand, if you rely on your skilled team members to make time in their day for preventive maintenance tasks, they could fall behind on their more complicated work.
Having a dedicated lube technician on your staff eliminates both problems. You’ll have more control over your schedule and the quality of the work. Work gets done when you need it — and to your standards.
2. They help you leverage skilled labor more effectively.
There’s no reason your diesel mechanics need to handle basic oil changes. A dedicated lube tech only needs simple training to do the job — and they’re a more economical option. Just look at the average hourly rates as of April 2025:
- Diesel mechanic: $281
- Service/lube technician: $171
A mechanic working on maintenance means you’re losing $11 an hour in efficiency. Shifting the work to a technician means you can increase billable hours and reduce burnout for your more skilled laborers. Plus, a dedicated tech can start to specialize in maintenance, learning OEM guidelines and increasing productivity.
3. They help you build for growth. Maximize ROI through efficiency
When it comes down to it, downtime is lost revenue. It’s that simple. A consistent schedule means you can plan around (or avoid) downtime related to preventive maintenance. It also helps your crews reduce the chances of wear-related equipment failures.
When you add a dedicated technician to the equation, you also create space for growth with no operational drag. That’s because your highly skilled crew members are focused on their work, not oil changes. The best part is that efficiency can compound. The more streamlined your workflow, the bigger your ROI can be.
Bonus tip: Maximize efficiency with a mobile lube system
Your future lube technician could be even more efficient if you set them up with a system engineered for on-site maintenance. Transporting equipment to and from a shop takes time, costs more and risks damage during the trip. Mobile lube systems eliminate all three issues, helping your technician focus on the job instead.
There are options for every budget and capacity need, including everything from small lube carts to lube trucks. Sage Oil Vac offers a full range of systems — without the hassle and extra maintenance related to traditional pump-based systems. Pump-free systems also faster, safer and cleaner, giving you even more advantages during preventive maintenance.
Here’s the Bottom Line
Hiring a dedicated mobile lube tech is about more than oil changes. It’s a strategic move for your business. Use it to:
- Boost uptime.
- Cut costs.
- Free up skilled labor.
- Reduce liability.
References
- ZipRecruiter. National average salaries as of April 2025.